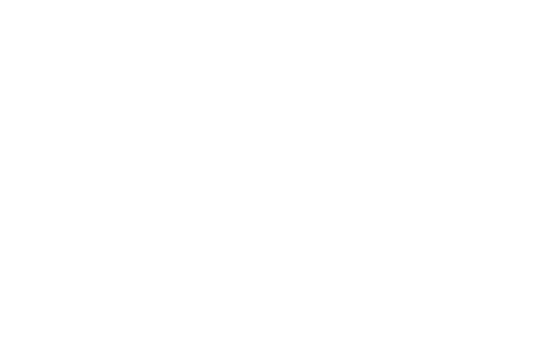
CEREAL SUCCESS
BVC, the market leader in cleaning solutions has completed an installation for a major cereal producer at one of their UK production facilities, installing a Centralised Vacuum Cleaning System within their raw materials silo/processing building.
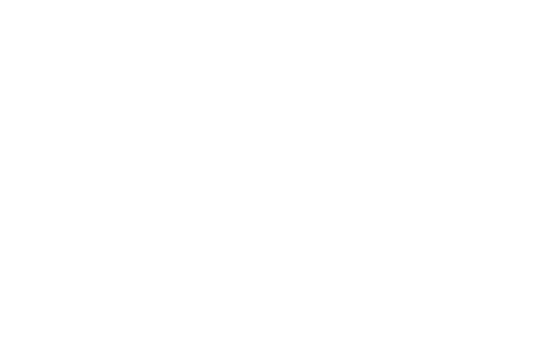
BVC, the market leader in cleaning solutions has completed an installation for a major cereal producer at one of their UK production facilities, installing a Centralised Vacuum Cleaning System within their raw materials silo/processing building.
The brief from the customer included:-
(A) Ensuring dust levels were minimised to meet the requirements of the area classification under the ATEX Directive.
(B) Ensuring cleanliness was acceptable to meet the stringent requirements of Health & Safety for the manufacture of foodstuffs.
(C) The provision of a system to serve a number of floor levels with the collection of product to a central location for ease of disposal.
The BVC solution:-Design for a single operator system using 51mm bore flexible hose and tools, suitable for removing organic grain dusts and small granulate. The 8 point system serves numerous floors from the silo tops, silo discharge, processing and sieving equipment down to the ground floor where product is transferred to production employing blow pots.The extracted materials are conveyed through the graduated pipe system, which is provided with long radius bends and ‘Y’ pieces all connected together using compression couplings back to the filter separator. Extracted materials are separated from the conveying air stream within the filter separator, which has fabric antistatic media cleaned by the reverse jet technique. These materials being dispensed when the system is not operating, using a manually operated valve into the clients FIBC’s below.
Due to the materials being extracted by the system being organically based products, there is a potential risk of an explosion occurring if the right conditions were to arise and therefore the filter separator is designed with a pre-determined vessel strength, sized according to the dirty air volume and material Kst value. This explosion panel is vented directly to atmosphere and is provided with a rupture indicator to shut down the system immediately if activated.Motive air for the system is generated by an exhauster package, which is powered by a 5.5 kW motor located on a self-tensioning drive arrangement, guard filter with pressure differential switch, all necessary auxiliaries. These are assembled within a forced draft acoustic enclosure, reducing noise emission levels to below 70 dB(A) at 1 metre measured under free field conditions.
The areas within the clients building are all classified ATEX Zone 22, with No Zone (Safe Area) externally to the building in which the plant has been installed.