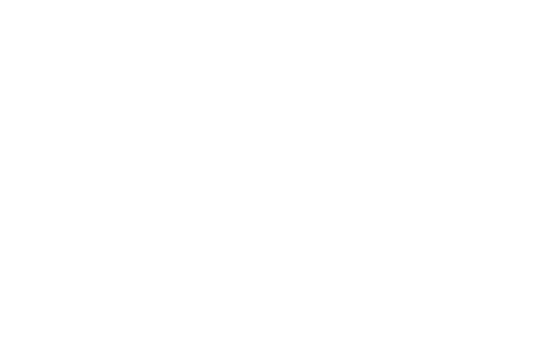
Full of beans
BVC have designed and installed a central vacuum cleaning / bulk removal system for an international food processing company. The areas from which products are cleaned up and the location of the exhauster, are within a ZONE 22 classified area under the ATEX Directive.
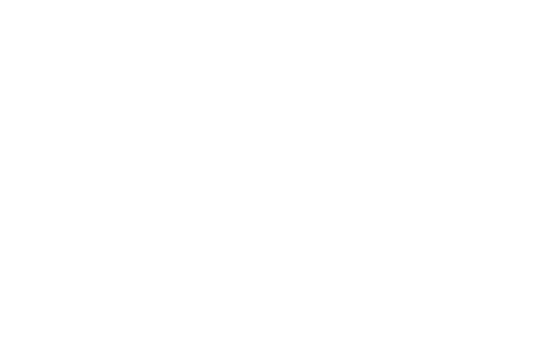
The system covers the product delivery conveyor, storage silo tops and bases through to the production building where the products are processed. The system removes beans, hulls and flaked materials conveying them to a filter separator via a rotary valve discharging them into the clientβs waste product skip.
The system enables 2 operators using 51 mm hoses and tools for general heavy industrial vacuum cleaning duties, with hose lengths up to 15 metres. In an area where spillages can occur the system can be used by a single operator using a 76 mm hose and aerator nozzle to carry out bulk removal duties.
Hose connection points are interconnected with a graduated mild steel pipe work system provided with long radius bends and branches connected to a filter separator, containing fabric filters. Reverse air jet cleaning is used to keep them in optimum working order. Due to the potentially explosive characteristics of the product dust, the filter vessel is fitted with an explosion relief panel, with a rupture indicator which shuts down the system if activated.
Motive conveying air is generated by a positive displacement exhauster powered by an 18.5 kW motor, fitted in a force draft acoustic enclosure, reducing the noise level down to below 70 dB(A) at 1 metre free field.
Located alongside the exhauster package is an electrical control panel enclosing the required exhauster and rotary valve starters providing sequenced operation of the system.