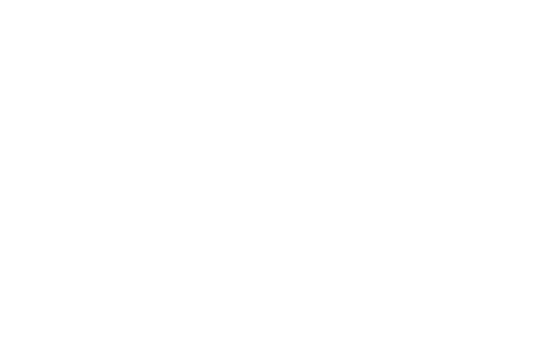
PET FOOD CLEAN UP
A major UK petfood producer has awarded Quirepace Limited a contract for the design and supply of a third BVC central vacuum cleaning system after two installations were completed a few years ago.
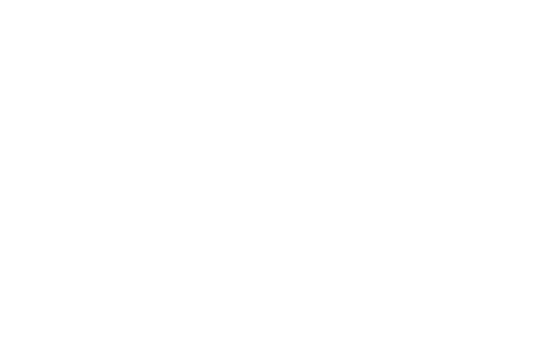
The first extensive central vacuum cleaning system serves IBC storage/conveying building and the adjacent kitchen multi-floor building. Due to the extensive area, the system is to serve the two areas which are isolated from one another prior to the filter separator located on a floor level high up in the kitchen building.
The two pipework systems were each designed for 3 people using 51mm hoses and tools for general cleaning of production equipment, floors, and building structure. The operators are distributed around the pipework system using a 7.5-metre length of hose which can be extended by a further 7.5-metre extension hose giving a maximum hose length of 15-metres from any of the hose connection points.
Over 1.3 kilometers of correctly sized and graduated pipework interconnects one hundred and fourteen
hose connection points, connected to the filter separator and exhauster package located 20 metres above ground floor level.
Extracted materials are separated from the conveying airstream and immediately dispensed from the vessel via a rotary valve to the clientโs bin located on the ground floor via a chute. As some of the materials being handled by the system have a potential explosion hazard the filter separator is provided with a flameless explosion protection unit enabling the pressures and hot gases generated by an explosion to be safely emitted to the surrounding area but preventing expulsion of burning matter, additionally, the rotary valve provides an autonomous flame path barrier preventing flame from passing in an explosion situation.
Motive conveying air for the system is generated by an exhauster located in a forced draft ventilated acoustic enclosure, the exhauster is powered by a 30.0 kw motor with emitted sound pressure level of below 77 dB(A) at 1 metre.
The system is provided with a sequenced control panel housing the necessary 3 phase motors and generates its own 24 vDC control voltage.
Whilst executing the first system Quirepace was engaged to design and supply a further system for their pre-extrusion facility. Not such an extensive system was required but still sized for 3 operators using 51 mm hoses and tools for general cleaning of production equipment, floors, and building structure. The operators are distributed around the pipework system using a 7.5 metre length of hose which can be extended by a further 7.5 metre extension hose giving a maximum hose length of 15 meters from any of the hose connection points.
The twenty hose connection points are interconnected with a correctly sized and graduated pipework to the filter separator and exhauster package, extracted materials are separated from the conveying airstream and immediately dispensed from the vessel via a rotary valve to the clientโs bin located on the ground floor via a chute.
The latest requirement is for another system to serve a new processing facility, again designed for 3 operators using 51 mm hoses and tools clean production equipment, building structure, and floor levels using a 7.5 metre operating hose with an extension hose of another 75. Metres give a maximum hose length of 15 metres from any of the hose connection points.
The fifteen hose connection points are interconnected with a correctly sized and graduated pipework to the filter separator and exhauster package, extracted materials are separated from the conveying airstream and immediately dispensed from the vessel via a rotary valve to the clientโs bin located on the ground floor via a chute.
Motive conveying air for the system is generated by an exhauster locating in a force draft ventilated acoustic enclosure, the exhauster is powered by an 18.5 kw motor with emitted sound pressure level of below 75 dB(A) at 1 metre.
The system is provided with a sequenced control panel housing the necessary 3 phase motors and generates its own 24 vDC control voltage.