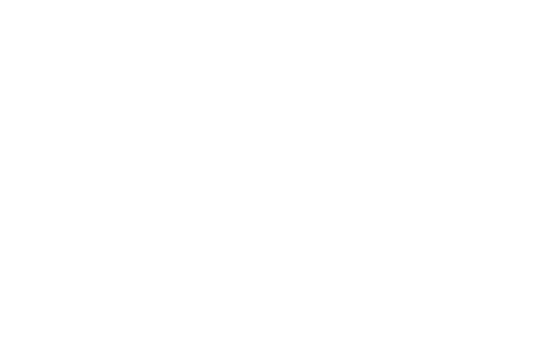
WELD SLAG REMOVED
Leaders in the market, Quirepace uses vacuum technologies in customised applications.
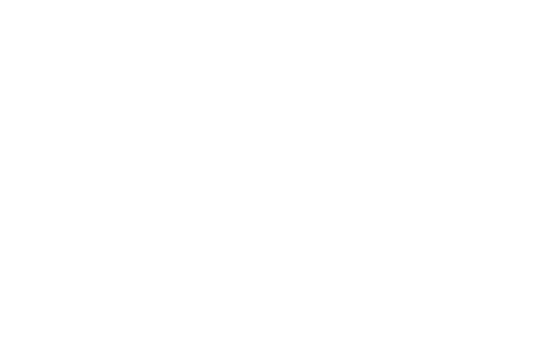
A global tube manufacturing company has built a size reduction and negative pressure lean phase handling system. The system’s main goal was to lessen the amount of waste that was moved further along the production line. This was accomplished by automatically transferring the finished welded product, which required manual campaign cleaning, which could only be done when the plant was not in use. With the Quirepace BVC system solution, production is no longer halted, and continuing cleaning expenses connected with employing an expensive vacuum plant have been removed.
The system consists of two stations into which the glassy abrasive material known as weld slag is supplied. From there, it is guided through a chute that directs it into the crusher machines.
To make sure it doesn’t obstruct the chosen conveying line, the slag lengths, which are 150/200 mm long, 25/50 mm wide, and 5–6 mm thick, are subsequently ground down to small granulate and dust.
Individual conveying lines that connect the two crusher stations to the filter separator and are separated from one another by pneumatic line isolating valves are used to connect the two crushing stations. Products are continually distributed from the filter separator through a pneumatically driven double dump valve into the customer’s skips, which are separated from the conveying air within the filter separator.
Since the client’s manufacturing process requires flexibility, either in terms of how many, which production lines, or both, must be used. As a result, the product removal method needs to be adaptable.
A 30kW exhauster unit that has an inverter drive produces the motive air; one extraction line can be served by operating the machine at one speed, and two extraction points may be served by running the machine at a higher speed.